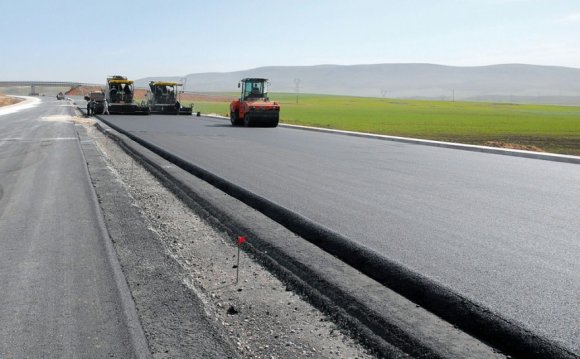
INTRODUCTION Scrap tire rubberized is integrated into asphalt paving blends utilizing two different ways, which are named the wet process together with dry procedure. Within the wet-process, crumb rubber will act as an asphalt cement modifier, while in the dried out process, granulated or ground plastic and/or crumb plastic is employed as a percentage of the good aggregate. In both cases, crumb rubber can be known as crumb plastic modifier (CRM) because its use modifies the properties for the resultant hot-mix asphalt concrete item. The dry process may be used for hot mix asphalt paving in dense-graded, open-graded, or gap-graded mixtures. It may not be utilized in various other asphalt paving programs, such as cold blend and processor chip seals or surface treatments. In dry procedure, granulated or ground rubberized and/or crumb rubberized is employed instead for a tiny percentage of the good aggregate (usually 1 to 3 percent by body weight of this total aggregate inside blend). The rubber particles tend to be combined with the aggregate ahead of the inclusion for the asphalt cement. Whenever tire rubber is used as some of the aggregate in hot mix asphalt cement, the resultant product might be known as rubber-modified asphalt concrete (RUMAC). The dry procedure made use of most frequently in america ended up being initially developed when you look at the late 1960's in Sweden and is marketed within country underneath the trade title PlusRide by EnviroTire. The PlusRide technology is a patented procedure. In this process, from 1 to 3 per cent granulated crumb plastic by weight of total mix is put into the paving mix. The granulated plastic is comprised of rubber particles varying in size from 4.2 mm (1/4 in) to 2.0 mm (No ten sieve). The target environment voids content regarding the asphalt mix is 2 to 4 %, that is often achieved at an asphalt binder content inside 7.5 to 9 per cent range.(1) a generic dried out process technology originated in the belated 1980's to very early 1990's to create dense-graded hot mixtures. This concept uses both coarse and fine crumb rubber to match aggregate gradings and to achieve enhanced binder customization. The crumb rubber might need a prereaction or pretreatment with a catalyst to reach maximum particle swelling. In this system, rubberized content does not exceed 2 per cent by fat of complete blend for area courses. Experimental pavement areas have now been put in Florida, nyc, Oregon, and Ontario.(2) The U.S. Army Corps of Engineers Cold areas analysis Engineering Laboratory (CRREL) investigated dry procedure CRM mixtures for disbonding ice on pavements. This analysis triggered a recommendation to put area parts with mixtures containing crumb plastic particles bigger than 4.75 mm (number 4 sieve), with a top measurements of 9.5 mm (3/8 in). The technology is called the amount rubber procedure.(2) Marshall properties, resistant modulus, and ice reduction examinations have already been carried out when you look at the laboratory with crumb rubberized levels of 3, 6, and 12 % by body weight of aggregate. Laboratory wheel screening shows that greater rubber content mixes could increase the incidence of ice cracking.(3) The chunk rubberized procedure hasn't up to now already been industry evaluated.(2) PERFORMANCE RECORD The reported performance of rubber-modified asphalt cement sidewalks has varied widely in numerous chapters of the United States. Listed here sentences summarize the experiences of selected states using the dried out procedure. The California Department of Transportation (CalTrans) has built four projects making use of the PlusRide dry process technology. Some stress in the form of cracking or flushing in wheel routes ended up being seen in three of the jobs, but total, CalTrans features stated that two regarding the four dry process projects have actually out-performed standard dense-graded asphalt, and a third task has performed comparably. A fourth task wasn't properly designed and required an overlay.(4) The Minnesota Department of Transportation (MNDOT) has actually utilized the dried out process in asphalt paving on a minimum two various jobs, beginning in 1979. The two dry procedure tasks had been both PlusRide installations, utilizing granulated crumb rubberized and a gap-graded aggregate so as to develop a self de-icing pavement.(5)The two PlusRide sections have performed well, but never have shown advantageous assets to counterbalance the increased cost, and have maybe not shown any considerable de-icing benefits.(5) |