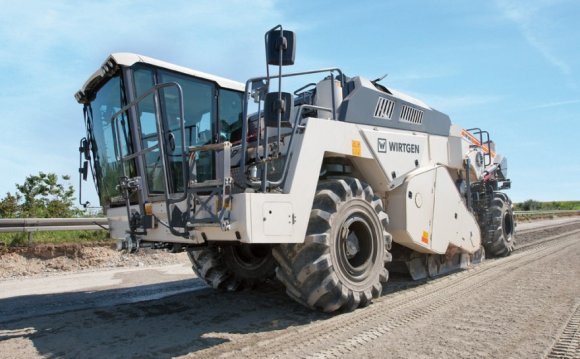
The energy package is not just essentially suitable for conform to appropriate provisions concerning the optimum total body weight of oversize transports however with its milling overall performance of 900 tonnes each hour in addition fully fulfills the high end needs of milling technicians. WIDIRVE machine managment system, which greatly improves operator comfort, electric ISC travel drive control, PTS system (brief for "parallel to area") and either three different milling drum speeds.
Know about the components of WIRTGEN big milling machines
-
Electrical system
- Emergency operation
Electrohydraulic power pack to boost device in emergency mode. - Digital camera system
Robust digital camera system including up to six cameras and up to two displays. - Job information
Precise recording of task data including “truck full” message.
More Information
- Emergency operation
-
Grip drive
- Hydraulic pre-tensioning of track stores
Hydraulically pre-tensioned track stores for enhanced procedure. - Grip control
Intelligent electronic traction control system for the track units. - Track rate modification
Electric adjustment of this track speed during cornering to ensure optimum traction and reasonable deterioration. - Four-fold full-floating axle
Four-fold full-floating axle for maximum machine security.
- Hydraulic pre-tensioning of track stores
-
Operator's system
- Multifunctional joystick
Multifunctional joystick with operating, steering, choosing operating mode, increasing device and changing down conveyor features. - Ergonomics
Ergonomically created, backlit controls for non-tiring, effective working. - Hydraulically going and swivelling operator’s cabin
Recommended Operator Comfort System (OCS) for a great working environment. - Protective canopy
Fixed defensive canopy with telescoping part panels for maximum defense against bad weather. - Parallel positioning of machine
Automated parallel positioning regarding the device both during the milling operation as well as in transportation mode.
Extra Information
- Multifunctional joystick
-
Milling drum device
- Locking of scraper blade
Automatic mechanical locking of scraper blade to make sure simple procedure. - FCS LIGHT
FCS Light when it comes to quick replacement of milling drums in FB2000 and FB2200 milling drum units. - HT22 quick-change toolholder system
Extra efficient, tried-and-tested HT22 quick-change toolholder system as standard equipment. - Right-hand part plate raise of 450 mm
Right-hand part dish may be raised by to 450 mm to allow flush-to-kerb milling within full milling depth. - Load-controlled liquid squirt system
Liquid spray system with automatic adjustment on milling overall performance for maximum device air conditioning. - Milling drum turning device
Drum switching device make it possible for cutting tool replacement with all the diesel motor switched off.
- Locking of scraper blade
-
Engine place
- Three various milling drum speed options
Three selectable cutting speeds for maximum millingperformance in an extensive range of applications. - Load-controlled lover rate
Fan rate influenced by engine temperature for low energy usage and reduced noise emission amounts.
- Three various milling drum speed options
-
Conveyor system
- Big slewing perspectives
Conveyor slewing perspectives of 60° to both edges to enhance the running procedure. - Tremendous conveying capability
High conveyor running capability and drive energy for extremely effcient material running. - Vacuum Cutting Program
Vacuum Cutting System for enhanced exposure. - Folding conveyor with fastener
Folding conveyor with smart mechanical fastener for simple transport.
- Big slewing perspectives
-
Machine frame
- Perfect visibility
Slender machine frame design in front including double wasp waist for a great view for the milling side. - Easy transportation
Easy transportation considering reduced device body weight and variable supplementary weights as much as 1, 700 kg.
More Information
- Perfect visibility
-
Levelling
- Big range of detectors
LEVEL PRO automated levelling system as standard equipment, supplying a big range of sensors and extremely precise control of the milling depth. - Milling depth indicator
Milling depth signal on the DEGREE professional display (showing difference between scraper blade and side dish jobs). - Scanning in front of the milling drum
Checking in front of the milling drum via hydraulic cylinders with integrated measuring system – ideal for use in addition utilizing the Multiplex system. - Automated system to begin the milling procedure
Automatic system to begin the milling procedure with load-controlled lowering rate.
- Big range of detectors
Detailed information regarding the W 220
Model | W 220 |
Milling width | 2, 200 mm7 ′ 3 ″ |
Milling level | 0 mm - 350 mm - 14 ″ |
Engine power | 571 kW / 777 PS571 kW / 766 HP |
Emission requirements | no EC regulation / United States Tier 2no EC legislation / United States Tier 2 |
Running fat, CE * | 36, 360 kg80, 160 pounds |
Quantity of crawler songs |
W 220 | Milling width 2, 200 mm7 ′ 3 ″ | Milling level 0 mm - 350 mm - 14 ″ | Engine energy 571 kW / 777 PS571 kW / 766 HP | Emission requirements no EC regulation / US Tier 2no EC regulation / US level 2 | Operating fat, CE * 36, 360 kg80, 160 lbs | Few crawler tracks 4 |
Cool milling device W 200 / W 200i
Lightweight 2-m device for efficient milling tasks
View productCool milling machine W 200 Hi
Compact huge milling device for double flush-to-kerb milling
See productCold milling machine W 210 / W 210i
Versatile high-performance milling machine for professional programs
View productCool milling machine W 215
Professional top performer for guaranteed milling success
See itemCool milling device W 250i
Top notch in performance and output
See item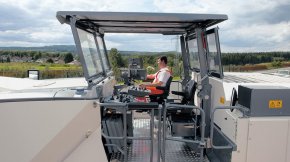
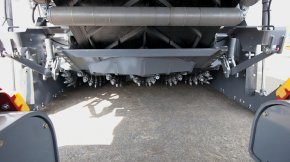
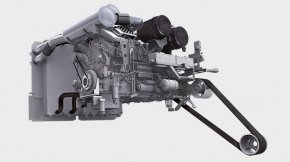
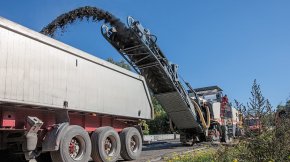