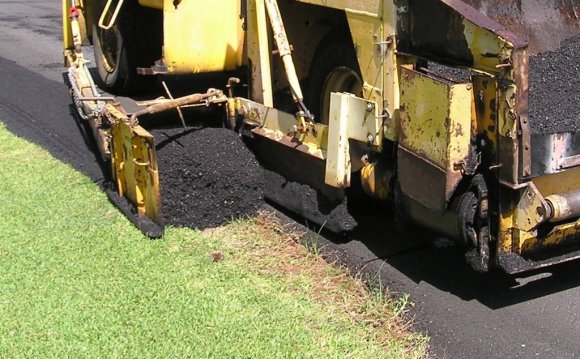
Although the business has actually moved focus to exactly how different mix designs can increase the lifetime of a pavement, a very important factor remains continual: the degree of compaction any asphalt blend obtains right impacts the standard and time of that pavement.
“The single primary action you can take to a pavement is small it, ” says Jim Scherocman, P.E. and annual speaker at National Pavement Expo. “A pavement that has the world’s best combine design compacted to 9-10per cent atmosphere voids isn't going to succeed. Alternatively, a pavement that features only a marginal combine design compacted to 7% atmosphere voids or less, will do well under traffic.”
Accepted understanding claims that for each and every 1per cent increase in environment voids, about 10per cent of this pavement life are lost. That’s because even more air voids a pavement has, the more that pavement is affected with regards to pavement energy, weakness life, durability, raveling, rutting and susceptibility to moisture harm.
And so the paving business hinges on compaction to increase pavement density to increase pavement life. Because of the compaction procedure, the asphalt-coated aggregate particles into the combine are forced closer together, which increases the amount of aggregate interlock and interparticle rubbing and in addition lowers the air void content of this blend.
"a frequent thickness level or environment void content is really what is really important, " Scherocman states. "the appropriate rolling design obtains uniform density, which achieves overall performance. The amount of atmosphere voids acquired during rolling has to be similar both longitudinally and transversely."
Therefore, the work carried out by roller providers has to be done correctly and regularly in order to ensure the success of the pavement life. In the event that operator actually working it at the right configurations, the right rate, etc., it could impact the quality of the mat, and that quality is essential on life of the street. The higher the operator, the greater the equipment, the greater the performance while the longer the life associated with the road.
5 Factors Impacting Thickness
There are five factors that affect finished density of the asphalt pad: heat of mix it self, pad width, base temperature, ecological conditions (air temperature), and wind.
“The two essential facets would be the temperature of combine because it passes from beneath the screed regarding the paver and depth for the level. The background atmosphere heat and heat of this surface by which the mix is put are of additional importance. Wind velocity, however, have a significant effect of the price of air conditioning aswell, ” Scherocman states.
Asphalt tangible mixtures fun rapidly therefore it’s crucial that you compact even though the combine is hot. Usually, asphalt happens for the plant at about 300° F. At that temperature, its fairly soft and it is easily compacted. Since it cools, it firms up-and compaction becomes more and more tough.
"the 3 essential aspects in terms of compaction tend to be temperature, temperature, heat. You need to compact the mix while it's hot, " Scherocman says. "make sure you keep consitently the rollers right behind the pavers, only 300 ft. right back. This may assist providers take advantage of the temperature.
Utilizing a Rolling Train
The most-common method of compaction, however the best, is a moving train, that involves a number of rollers running one following the various other close behind the paver. The train begins with a double drum vibratory roller running close behind the paver to search for the initial compactive work although the mix is still hot.
a guideline is it “breakdown” moving must be finished before the area temperature associated with the mix drops below 240o F. The description roller ought to be managed at the maximum frequency level designed for the specific make and model of roller at an amplitude environment which dependent on the depth regarding the asphalt cement pad being put (see sidebar).
"Vibrate every opportunity it is possible to, " Scherocman states. "The harder and more often you strike the pavement, the more density you receive."
Another the main train, intermediate rolling, is usually finished with a vibratory roller besides and must be accomplished right after the initial rolling is finished. When a pneumatic tire roller is employed as an intermediate roller, it is important to keep the tires during the same temperature as mat being compacted – usually the rubber tires will pick up a few of the blend from the mat. So when making use of a pneumatic roller, don’t permit the roller to sit and wait for long periods of time given that tires will cool off.
The ultimate roller when you look at the train is a static metal wheel roller for finish rolling. The main function of complete rolling should obtain the “last little bit" of density also to take away the markings, if any, left by the very first and second rollers. When needed finish rolling should be achieved at a combination surface heat above 175° F. "Only the finish rolling, the final rolling done, ought to be done in a static mode, " Scherocman says.
The Impact of Roller Speed
The rate of which the operator pushes the vibratory roller comes with one of the biggest impacts on mat high quality. Driving too fast can leave spaces and ripples in compaction and compromise team protection if operator gets also close to the paver. Utilizing the correct rate will also help to maintain the appropriate impact spacing to stop washboarding.
"there's a commitment between speed and regularity, " Scherocman claims. "you intend to hit the pavement utilizing the vibratory roller drum about 10 times in a linear base. It is not simply the speed by itself, it is the mix of speed and regularity for the vibratory rollers."
Therefore a vibratory roller operated at a frequency of 3, 000 oscillations each minute (vpm) can operate at a rate of 3.5 mph to keep up a visible impact spacing of 10 impacts per base. If that same roller is managed at a frequency of 4, 000 vpm it can run at a speed of around 4.7 miles per hour and still keep an effect spacing of 10 impacts per base.
Operators should avoid razor-sharp turns or abrupt rate modifications. Sharp transforms can tear the mat, and decelerating or accelerating rapidly can rip or tear the mat or keep indentations.
3 Heat Zones
Scherocman claims contractors need to focus on, and take advantage of, the three temperature areas present many asphalt tangible mixes.
In the 1st, or top, temperature zone, the asphalt concrete mix is fairly stable during compaction procedure. This security stretches from laydown temperature (300° F) down to approximately 240° F where the mix stays steady and can support compaction – the mix won’t shove or check under the roller.