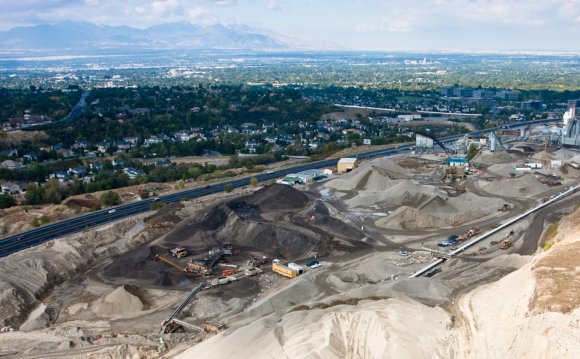
Something has arrived involving the asphalt vehicle and also the paver. It’s labeled as a material transfer vehicle (MTV), plus it’s leading the move towards a smoother surface condition inspectors and the motoring public tend to be demanding nowadays.
The MTV sits in the middle of the paving process, directly behind the vehicle and in front side of the paver. In the past, the truck and paver worked side-by-side to get the task done, but every rise or vehicle change typically triggered a bump within the roadway. The MTV, which pulls product from the vehicle and directs it on paver, acts as the buffer. Some have a certain amount of surge ability, which will keep the paver moving if the after that round of vehicles is sluggish in enabling to your work site.
“You’re gonna see tremendous growth in the transfer material market, anything from shuttle buggies, to mobile conveyors, to pickup materials, ” stated David Salzmann, marketing and advertising supervisor for Pro-Pav. “Non-contact paving is really what everyone is aiming at. When (state inspectors) come down the trail with a profilograph and start calculating deviations, you’ll see one every time you change trucks. (MTVs) keep consitently the trucks from experience of the paver.”
Incentive paving is just starting to get fire. Even more states tend to be getting off technique requirements, in which technicians are informed what type of gear is to be used on the job to achieve a finish result, to performance specifications, which award or penalize on the basis of the top-notch work this is certainly done.
“There’s going to be a continued drive to give the machines the capability to pave smoother, ” Caterpillar item supervisor Bob Ringwelski said. “The pressure is coming from the proven fact that now there is an added bonus tangled up in it, and plenty of contractors depend on the bonus for profit.”
MTV technology is not precisely a new comer to Roadtec. In accordance with Jeff Richmond, vice-president of sales and advertising, the company “pioneered the move ten years ago.”
The industry is addicted to
sonics, and with that comes a weightier dependency on electronics. Pavers today incorporate sonic automation, or sensors, to monitor class and pitch settings, eliminating the employment of a physical component coming in contact with the pavement. Helping the sensor techonology are microprocessors, which carry the computer system needed to carry out all measuring and modifying.
All the hype originates from a paver marketplace that is booming, thanks to the Transportation Equity Act of twenty-first Century.
“i might must trust my competitors once I state it’s the best marketplace we’ve seen in a lengthy, long-time, ” stated Richmond.
Huge in proportions, large in quantity
And there is a large number of rivals with a say in production of huge and mid-sized pavers, including Roadtec, Caterpillar, Blaw-Knox, Pro-Pav, Propaver, Cedarapids, Dynapac and Midland.
Blaw-Knox
Blaw-Knox, manufactured by Ingersoll-Rand, Mattoon, Ill., hits the road with two new pavers: the wheel-mounted PF-2181 and track-mounted PF-4410.
The PF-2181 is an 8-ft asphalt paver-finisher with a maximum paving width convenience of 21 ft. Powered by a Cummins 6BT 5.9 turbo-charged diesel engine that yields 145 hp at 2, 100 rpm, the design is equipped with a two-speed hydrostatic direct grip drive system which gets rid of 70%of technical drive-train componentry and provides paving increases to 260 ft per minute.
Paving widths all the way to 25 ft may be accomplished utilizing the PF-4410, which also comes with a Cummins 6BT 5.9 turbo-charged diesel motor and hydrostatic direct grip drive. Screed alternatives include both fixed width and energy extendible 8-ft devices.
Caterpillar
Laying track for Caterpillar is a fleet which includes the AP-1055B, AP-650B while the AP-1000B.
The AP-650B is the brand-new kid when you look at the business’s 8-ft asphalt paver class. The design adds a track paver into Caterpillar range, and is driven by a Cat 3054TA turbo-charged, after-cooled diesel motor that kicks aside 121 hp. Maximum pave speed is 220 ft each and every minute. The key to just what the company calls a “smoother ride” could be the triple-roller rear bogey, which combines three units of wheels into one bogey that evenly distributes the weight associated with the machine as well as the screed throughout the period of each track. Outboard feeder drives enable a narrower center chain cover, causing much better material flow to the augers.
Cat’s Mobil-trac undercarriage shows the AP-1055 paver. The Mobil-trac system combines the grip and flotation advantages of a track suspension utilizing the flexibility and ride quality of a rubber tire paver. The device can achieve paving speeds as high as 200 ft each and every minute and travel speeds of up to 10 mph.
The control system for the AP-1000B’s conveyor and auger drive removes feeder gates to regulate product amount. The conveyor-to-auger speed proportion are adjusted to give specific amounts of material, leading to slowly running feeders that operate high in asphalt. The device also precisely maintains blend amounts when you look at the auger chamber after all screed widths. Containing a Cat 3116TA turbo-charged, after-cooled diesel motor that creates 174 hp, the paver is driven by a hydrostatic propel system with four rate ranges.
A deceleration pedal, hydraulically flexible augers and a rate control system are features available on all three models. The decel pedal enables the operator to manage rate with a base pedal, leaving both hands absolve to steer and control other features, even though the rate control system enables consistent rate is maintained throughout the work.
Cedarapids
Cedarapids latest idea may be the Smartrac program. On the business’s Grayhound Rubber Track Pavers, the machine is friction driven and incorporates the business’s branded self-adjusting track tensioning system, three-point suspension, framework raise system, oscillating bogie wheel assemblies and a wider position.
The self-adjusting track tensioning system preserves correct track stress all the time, and given that it’s hydraulically managed and self-charging there is no need for manual modification.
Oscillating, rubber-coated bogie wheel assemblies are pivot attached to a heavy-duty frame, plus in conjunction using the three-point suspension maintain maximum track contact for a smoother operator trip and a greater quality mat.
The three-point suspension system system isolates track action from remaining portion of the paver, causing a smoother mat, much more uniform track loading, enhanced tractive energy and offered track element life, in accordance with the company.